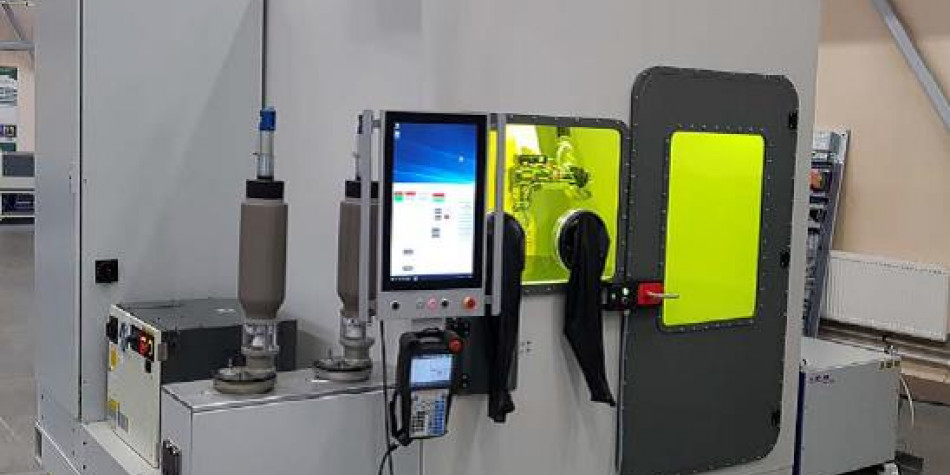
По типу процесса (методу синтеза) аддитивное производство металлических изделий можно разделить на две группы: послойное селективное выращивание предварительно нанесённого материала и прямое выращивание, последнее подходит для изготовления крупногабаритных деталей, в том числе судового машиностроения. При прямом выращивании наплавочный материал, который может быть в виде металлического порошка или проволоки, подаётся в зону действия мощного источника тепла, нагревается, расплавляется, охлаждается и после кристаллизации образует валик, геометрические характеристики которого соответствуют определённому слою 3D модели. Источниками нагрева могут быть лазерный или электронный луч, а также электрическая дуга.
По сравнению с литьем и сваркой технология прямого лазерного выращивания элементов судовых движителей сложной геометрической формы в перспективе даёт следующие преимущества:
- возможность управления не только внешней геометрией элементов, но и внутренней структурой, что позволит создавать облегченные конструкции с локальными силовыми элементами, позволяя более рационально использовать материалы, а также облегчить конструкции силовых движителей в целом;
- возможность формирования элементов из разнородных материалов;
- более высокое качество элементов, к которым предъявляются требования по герметичности, за счет получения структуры с минимальной пористостью (или без нее);
- высокий коэффициент использования материалов за счет минимизации объема окончательной механической обработки благодаря уменьшению технологических припусков на последующую механическую обработку;
- отсутствие необходимости создания дополнительной технологической оснастки (литейной, сварочной), что позволит сократить затраты, особенно в условиях единичного и мелкосерийного производства;
- сокращение сроков создания элементов опытных образцов судовых движителей.
Кроме того, при прямом лазерном выращивании операции механической, термической и дробеструйной обработки производятся на уже полностью выращенном изделии, значит, при серийном изготовлении данные операции можно производить параллельно. При этом мощность производства может быть увеличена в 1,78 раза.
Группа ученых Санкт-Петербургского государственного морского технического университета под руководством заместителя директора по научной и проектной деятельности ИЛИСТ СПбГМТУ, канд.техн.н. Е. В. Землякова в составе ответственного исполнителя младшего научного сотрудника